FDM 3D Printing Kynar® PVDF - Cost Effective Method to Manufacture Lab Consumables, Equipment, and Components In-House?
Overview:
PVDF is a unique member of the thermoplastic fluoropolymer family. PVDF has been used for decades in many specialized industries and is more commonly known by its trade name, Kynar® (Kynar® is the registered trademark of Arkema Inc.). PVDF is one of the highest purity thermoplastics in the fluoropolymer family. Therefore, PVDF is the material of choice for the food, cosmetic, biomedical, pharmaceutical, and chemical industries where the upmost level of quality control is required. Kynar® is USP VI compliant, FDA compliant, Kosher, and meets ISO 10993 requirements.
In recent years, Arkema has tailored PVDF for use in 3D printing/additive manufacturing applications. Companies, such as Nile Polymers and 3DXTech, have become industry leaders in making affordable PVDF filaments commercially available. These recent advances have made it possible for anyone with an FDM 3D printer to easily print Arkema’s Kynar® PVDF in their own homes and businesses. The ability for one to easily print PVDF is what sparked my interest in 3D printing.
I ventured into additive manufacturing with the sole intention of learning the ropes and working my way up to Kynar®. PVDF demonstrates superior chemical resistance and is chemically inert to most chemicals. Therefore, PVDF is commonly used in many fields of chemistry. I have always found it a struggle to justify the purchase of small PTFE or PVDF fittings/components, given their commercial price. The ability to 3D print these components in-house is both economically sound and practical. These in-house capabilities should be commonplace in laboratories, universities, and small businesses; with a 3D printer and PVDF filament, one has the ability to make their own components inexpensively, as the need arises. Furthermore, one can manufacture unique components with the equivalent properties of respective commercial items in a short period of time.
There are several types of commercially available PVDF filaments, including the PVDF homopolymer and the PVDF copolymer (Poly(vinylidene fluoride-co-hexafluoropropylene)).
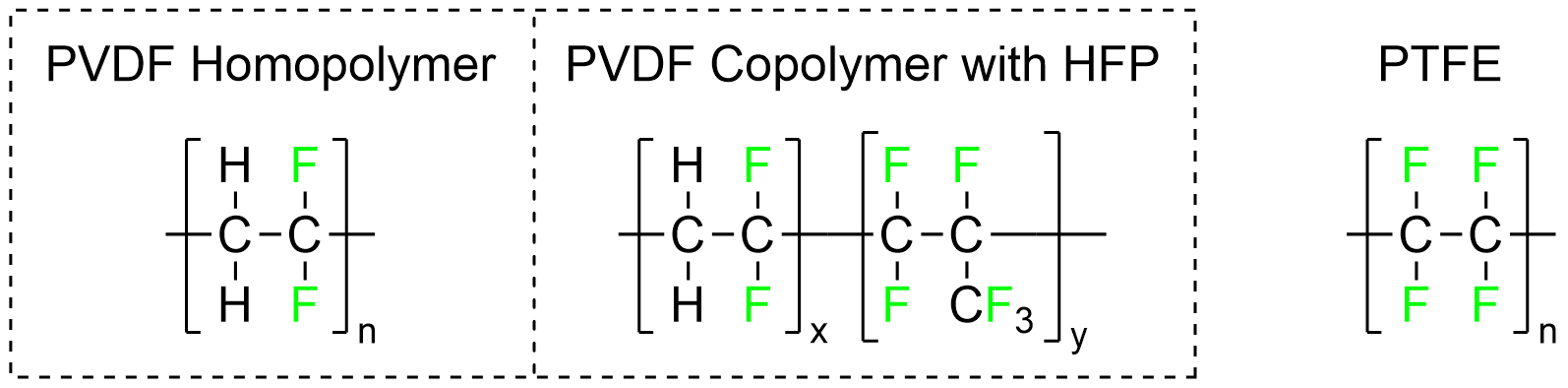
I was able to obtain two different types of PVDF:
FluorX™ PVDF Filament from 3DXTech (made using Arkema Kynar® PVDF) - FluorX™ is a Trademark of 3DXTech LLC.
Fluorinar-C® Kynar® PVDF Filament Poly(vinylidene fluoride-co-hexafluoropropylene) from Nile Polymers (made using Arkema Kynar® PVDF) - Fluorinar-C® is a Registered Trademark of Nile Polymers.
I have printed several PVDF components made for chemical and R&D applications and have tested them in a variety of circumstances. Ultimately, I found that PVDF is a viable alternative to commercially available fluoropolymer final goods. I propose that 3D printing PVDF is a revolutionary and cost-effective method to create lab consumables, equipment, and components in-house. In this blog, we seek to demonstrate the strengths and unique properties of 3D printed PVDF filaments, as well as exemplify their realistic applications and remarkable utility.
Background on PVDF:
PVDF has been in use for more than a half-century, since its invention by DuPont in the late 1940s. The widespread use of PVDF occurred in the 1960s, namely after the discovery of its unique piezoelectric properties. PVDF is widely used in the semiconductor industry as a result of these unique properties. The chemical properties of PVDF make it a top choice for use in the chemical industry. Furthermore, it has seen widespread use in the biomedical, pharmaceutical, healthcare, and food industries due to its high purity and FDA compliance. PVDF has been traditionally used to manufacture parts through melt casting, solution casting, spin coating, and film casting. Recently, Arkema has made it possible to manufacture items using PVDF filaments via FDM 3D printing. They state in their 2017 patent,
“There is a need for processes and/or formulations allowing for acceptable 3-D printing of crystalline fluoropolymer articles. Fluoropolymer articles are desirable in 3-D printing for their chemical resistance, durability, flame resistance, and mechanical properties. Fluoropolymers such as PVDF that can be printed with little warpage and part shrinkage are highly desired. Such materials could be used in the industry for prototyping and custom end-use parts where high chemical resistance, durability, and part integrity are needed.
Surprisingly, after much research, a semi-crystalline fluoropolymer and process conditions have now been developed, that can be used in a filament 3-D printing process with good resistance to shrinkage and warpage. Additionally, the fluoropolymer or fluoropolymer formulation provides high chemical resistance, high water resistance, hydrophobicity, thermal and UV resistance, high layer to layer adhesion, good use temperature, good mechanical properties, high Relative Thermal Index (RTI) rating (130-150°C), flame resistance, high elongation to break, and high impact, with the mechanical strength and stiffness that varies with the comonomer level in the PVDF, formulation components, filler type/level, and printing conditions. 3-D articles and parts printed from these formulations and using the methods of the invention could be stiff or flexible, with improved print resolution, and approach the strength and elongation to break of injection molded fluoropolymer parts. Filament made of the composition of the invention, due to its excellent moisture resistance, has a long shelf life of over a year, without any special moisture-resistant packaging.”¹
The geometric conformation of the PVDF homopolymer can be altered to provide different crystal structures, each with unique properties and specialized applications. PVDF can also be supplemented with a copolymer to give it unique properties, such as Fluorinar-C® - Poly(vinylidene fluoride-co-hexafluoropropylene). The piezoelectric properties of PVDF can be altered by supplementing it with various materials. One such example is the incorporation of graphene to produce Fluorinar-ESD™.
Example of Utility:
My interest in PVDF stems from its unique chemical properties and its potential as an alternative to expensive PTFE fittings and components, which are commonly used in chemistry laboratories. Some time ago, I needed a 10/18 inlet thermometer adapter to fit a thermometer into a short path distillation head. I looked at commercial products and found several potential options. Unfortunately, there were no readily available glass adapters that would fit 7.0 mm diameter red alcohol thermometers. A glass adapter would have to be paper thin to fit these thermometers, therefore glass was not feasible for this application.
The options were to purchase a fused/jointed thermometer, purchase a new short path distillation head with a different ground glass joint size, or purchase a thermometer probe and accompanying 10/18 inlet thermometer adapter fitted for the thermometer probe. The remaining option was to purchase an expensive 10/18 PTFE inlet thermometer adapter. I opted to improvise and used a rubber stopper to carry out the distillation without a thermometer. Subsequently, I purchasing a PTFE Chemglass CG-1048-04 Inlet Thermometer Adapter for this specific application. At the time, the PTFE Chemglass CG-1048-04 Inlet Thermometer Adapter cost something like $65 and took over a week to ship. This shipping delay itself would have been disastrous to the experiment and the crude solution would have likely degraded before the arrival of the adapter, prompting a repeat of the entire experiment. Furthermore, when the 10/18 adapter arrived, I was astonished by how thin and small it was. It had to be thin to serve its function, but it was surprising that the adapter cost $65 for weighing only 7.77 grams fully assembled.
The prospect of being able to print expensive chemistry components using PVDF was groundbreaking; having this capability would allow me to make components in a matter of hours, save large sums of money, and avoid lengthy shipping delays. Therefore, I designed and manufactured my own custom 10/18 inlet thermometer adapters using various types of PVDF to test its feasibility as an alternative to commercially available PTFE inlet thermometer adapters.
Below: PTFE Chemglass CG-1048-04 Inlet Thermometer Adapter.
Below: custom 3D printed 10/18 inlet thermometer adapter made using FluorX™ PVDF Filament from 3DXTech.
Below: custom 3D printed 10/18 inlet thermometer adapter made using Fluorinar-C® PVDF Filament from Nile Polymers.
As one can see from the pictures, it is possible to successfully 3D print functional PVDF components, which rival their commercial PTFE equivalents. It was surprisingly easy to make very thin and intricate components without expensive equipment. The custom 10/18 inlet thermometer adapters were designed from scratch using free online open-source software. Likewise, the custom inlet adapters were printed using an Ender 3 V2 FDM printer equipped with an E3D V6 All-Metal Hot End; a budget 3D printer which can be operated by a beginner and can be conveniently upgraded. PVDF filaments can even be printed with stock Creality Ender Series FDM printers, as the extrusion temp of PVDF is approximately 250 °C: within range of the maximum operating temperature of stock Ender Series hotends. Additionally, these components were printed with a simple enclosure and they did not require an expensive heated chamber. This is only possible due to the incredible warp resistance of PVDF filaments, such as Fluorinar-C®. Finally, this demonstrates the utility of FDM printing, as one is not required to maintain a physical stock of items and one can manufacture components as needed.
The custom 10/18 inlet thermometer adapter made using FluorX™ PVDF Filament from 3DXTech weighed 4.18 grams fully assembled and functioned exceptionally well for its intended usage. The PVDF homopolymer is a bit more difficult to print with and it takes some time to dial in the settings. The reported typical density of the PVDF homopolymer is 1.71 g/cc and the material itself is somewhat transparent compared to the copolymer.²
The custom 10/18 inlet thermometer adapter made using Fluorinar-C® PVDF Filament from Nile Polymers weighed 4.36 grams fully assembled. This material also functioned exceptionally well for its intended usage. The PVDF-HFP copolymer has a reported specific gravity of 1.78-1.80 g/cc and the material is a solid white color, resembling PTFE.³
The weight differences between the PVDF homopolymer and copolymer can be directly attributed to the differences in density. If one multiplies the density ratio of Fluorinar-C® PVDF to FluorX™ PVDF by the weight of the 10/18 inlet thermometer adapter made using FluorX™ PVDF, one obtains the approximate weight of the 10/18 inlet thermometer adapter made using Fluorinar-C® PVDF:
(1.78 g/cc)/(1.71 g/cc) = 1.041 ratio × 4.18 g = 4.35 g
The measured 4.36 gram weight of the 10/18 inlet thermometer adapter made using Fluorinar-C® PVDF falls within the calculated approximate weight range of 4.35 - 4.40 grams.
The inlet thermometer adapters manufactured from both types of PVDF effectively seal when placed in a ground glass joint and prevent liquids and solvents from leaking. They are able to hold up to 660-730 mmHg when placed under high vacuum.
Below: leftmost picture shows custom 3D printed 10/18 inlet thermometer adapters made using FluorX™ PVDF(left) and Fluorinar-C® PVDF(Right) from Nile Polymers. The second and third pictures from the left showcase a 10/18 and a 24/25 custom inlet thermometer adapter made using Fluorinar-C® PVDF, respectively. The rightmost picture depicts a custom 24/25 inlet thermometer adapter placed in a round bottom flask with a 24/29 ground glass joint, filled with water, and inverted. The custom 24/25 Fluorinar-C® PVDF inlet adapter seals perfectly and prevents water from escaping.
Below: custom 24/25 inlet thermometer adapter manufactured using Fluorinar-C® PVDF placed in apparatus under vacuum. Dow Corning® High-Vacuum Grease was utilized to improve seal.
Utility in Manufacturing Lab Consumables:
The slightly higher density Fluorinar-C® PVDF Filament makes it useful for more applications than the PVDF homopolymer. Namely, the PVDF-HFP copolymer allows one to manufacture thin items, such as a scoopula. The scoopula printed with the PVDF homopolymer was too flexible for practical usage, while the same scoopula printed with the PVDF-HFP copolymer was rigid enough for practical usage. Likewise, the PVDF-HFP copolymer was much easier to print due to its warp resistance. The Fluorinar-C® PVDF scoopula weighed approximately 3.35 grams and costed less than a dollar to manufacture. This makes PVDF an ideal material for crafting lab consumables; PVDF is FDA compliant, highly chemical resistant, and fairly inexpensive. The cost of a standard stainless steel scoopula is between $2.25-3.50. Likewise, stainless steel can corrode when exposed to strong acids and other corrosive chemicals, unlike PVDF.
Below: custom 3D printed scoopula made using Fluorinar-C® PVDF Filament from Nile Polymers. The first picture on the left shows a standard stainless steel scoopula, PETG scoopula, and Fluorinar-C® PVDF scoopula (left to right).
Utility in Manufacturing Lab Components:
Unlimited laboratory components and equipment can also be manufactured using PVDF. Many of these components can be used for biomedical, pharmaceutical, medical, food, and cosmetic industry applications. Common examples include Luer-Lock fittings, medical tubing adapters, hose barb fittings, impellers, containers, and threaded caps for vials and bottles. Furthermore, PVDF is autoclavable and can be used for processes which require sterilization.
Below: (right) which Kynar® barb adapter is 3D printed?
Nile Polymers has a great collection of items on Thingiverse, which show the wide range of applications of PVDF.⁴ I came across their Thingiverse designs page and found their “2 Inch Diameter Three-Blade Prop”, which was exactly what I needed for an impeller blade for an overhead stirrer.⁵ I decided to print their design using both FluorX™ PVDF and Fluorinar-C® PVDF filaments. I am very grateful to Nile Polymers for placing their design in the public domain.
Below: 2 Inch Diameter Three-Blade Prop from Nile Polymers printed using FluorX™ PVDF filament (top row) and Fluorinar-C® PVDF filament (bottom row).
Summary:
Thanks to Arkema, one now has the ability to affordably 3D print PVDF. Companies like Nile Polymers have made it commercially affordable to obtain many types of PVDF filaments. PVDF is absolutely amazing, no doubt about it. I am fully convinced that FDM 3D printing applications using PVDF filaments offer unlimited utilitarian potential. I have thoroughly tested the PVDF homopolymer and PVDF-HFP copolymer under extreme chemical and physical conditions and they both surpassed my initial expectations. PVDF is a great material and is highly applicable to specialized roles in many industries. There exists unlimited potential for FDM printed PVDF to solve real-world problems.
FluorX™ PVDF Filament from 3DXTech (PVDF homopolymer) was the first type of PVDF I was able to purchase and experiment with. There was a steep learning curve that had to be overcome to get this unique fluoropolymer to print properly. I became entranced with the utility of PVDF after I was able to successfully print this material. I highly recommend PVDF filaments to anyone who wants to manufacture their own lab equipment or functional prototypes. The homopolymer is a bit more difficult to print than the PVDF-HFP copolymer, which I realized after I began to experiment with the HFP copolymer. Either way, the homopolymer is an excellent material which demonstrates excellent chemical resistance and numerous unique properties. The PVDF homopolymer can also be purchased from Nile Polymers, as Fluorinar-H™ Kynar® PVDF Filament.⁶
Fluorinar-C® Kynar® PVDF Filament from Nile Polymers is much easier to print than the homopolymer, as it is less prone to warping and doesn’t require use of a brim to adhere to the build plate. It has a higher density than the homopolymer and is somewhat more rigid, allowing one to print thin, functional items. I really like the color of Fluorinar-C® PVDF, as it more closely resembles PTFE. It is highly chemical resistant and can be used in most laboratory conditions. Nile Polymers offers several different types of PVDF filaments, including their Fluorinar-C® Kynar® PVDF Filament, as well as 3D printing services.⁷ Visit their website at https://nilepolymers.com/ to take a look at their excellent products and services. I found great utility in the content on their website, as it was the only source for Cura profile settings for printing PVDF that I could find.
Ultimately, I love both the PVDF homopolymer and the PVDF-HFP copolymer and it is difficult to choose a favorite. They each have their own unique advantages and properties. If I had to pick a favorite, I would choose Fluorinar-C® Kynar® PVDF Filament from Nile Polymers due to its greater ease of printing, decreased warping, and ability to stick to the build plate without using a brim. Additionally, I like the color, texture, and slightly higher stiffness of the PVDF-HFP copolymer.
You can purchase different PVDF inlet adapters on this website’s products page. Click the URL Below!
https://www.tetragrowth.solutions/products
References:
Liu, David Shin-Ren; O'Brien, Gregory S.; Seiler, David A.; Aubart, Mark; Henry, James J.; Roland, Thomas. 3-D Printed Fluoropolymer Structures. WO 2017/173258 Al, October 5, 2017.
https://www.3dxtech.com/wp-content/uploads/2021/03/Unfilled_PVDF_v03.pdf
https://nilepolymers.com/wp-content/uploads/2019/05/Fluorinar-C-TDS.pdf
Special thanks to Dr. Howard Fisher, Materials Engineer and Co-Founder of Nile Polymers, for his generous donation of a large sample of Fluorinar-C® PVDF Filament.
Kynar® is the Registered Trademark of Arkema Inc.
FluorX™ is a Trademark of 3DXTech LLC
Fluorinar-C® is a Registered Trademark of Nile Polymers.